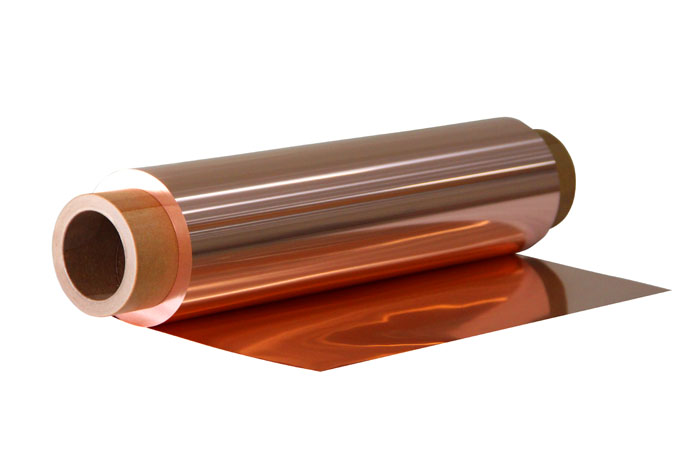
Rolled copper foil, a spherical structured metal foil, is manufactured and produced by the physical rolling method, its producing process as following:
Ingoting: The raw material is loaded into a melting furnace to be cast into a square column-shaped ingot. This process determines the material of the final product. In the case of copper alloy products, other metals besides copper will be fused in this process.
↓
Rough(Hot) Rolling: The ingot is heated and rolled into a coiled intermediate product.
↓
Acid Pickling: The intermediate product after rough rolling is cleaned with a weak acid solution in order to remove the oxide layer and impurities on the surface of the material.
↓
Precision(Cold) Rolling: The cleaned strip intermediate product is further rolled until it is rolled to the final required thickness. As the copper material in the rolling process, its own material hardness will become hard, too hard material is difficult for rolling, so when the material reaches a certain hardness, it will be intermediate annealing to reduce the material hardness, in order to facilitate rolling. At the same time, in order to avoid the rolls in the rolling process on the surface of the material caused by too deep embossing, high-end mills will be put between the material and the rolls in the oil film, the purpose is to make the final product surface finish higher.
↓
Degreasing: This step is only available in high-end products, the purpose is to clean the mechanical grease brought into the material during the rolling process. In the cleaning process, the oxidation resistance treatment at room temperature (also called passivation treatment) is usually carried out, i.e. passivation agent is put in the cleaning solution to slow down the oxidation and discoloration of copper foil at room temperature.
↓
Annealing: The internal crystallization of copper material by heating at high temperature, thus reducing its hardness.
↓
Roughening(Optional): The surface of copper foil is roughened (usually copper powder or cobalt-nickel powder is sprayed on the surface of copper foil and then cured) to increase the roughness of copper foil (to strengthen its peel strength). In this process, the shiny surface is also treated with a high-temperature oxidation treatment (electroplated with a layer of metal) to increase the material's ability to work at high temperatures without oxidation and discoloration.
(Note: This process is generally performed only when there is a need for such material)
↓
Slitting: the rolled copper foil material is divided into the required width according to the customer's requirements.
↓
Testing: Cut a few samples from the finished roll for testing of composition, tensile strength, elongation, tolerance, peel strength, roughness, finish and customer requirements to ensure that the product is qualified.
↓
Packing: Pack the finished products that meet the regulations in batches into boxes.
Post time: Jul-08-2021